电动汽车@@电池管理系统使用柔性@@ PCB 时@@,激光焊接产生的机械应力和温度@@变化会导致表面贴装@@ NTC 热敏电阻@@热开裂@@@@,这是一种难以预测的潜在严重故障@@@@。采用软端子和块状金属氧化物工艺的贴片热敏电阻@@可最大限度减小@@188足彩外围@@app 开裂@@的风险@@。
简介@@
随着电动汽车@@@@ (EV) 市场的持续快速增长@@,技术@@挑战和为应对@@这些@@挑战而开发的创新也在不断发展@@。在这些@@挑战和创新当中@@,改进电池技术@@@@、提高@@电源电路效率和快速充电解决方案@@是设计工程师最为关注的领域@@。
目前@@,电动汽车@@主要使用锂离子电池@@,单体电池电压为@@ 3.6 V 至@@ 3.7 V。因此@@,建立一个总电压为@@ 500 V 至@@ 900 V 的动力系统需要串并联数百个这样的电池@@。此外@@,优化如此多电池单元构成的系统的性能需要高效电池管理系统@@ (BMS),这种系统必须能够监测电池的温度@@@@、阻抗@@ (电池内阻@@)、电压以及充放电电流@@。其中每项指标都会影响电池的性能@@。
NTC 对@@ BMS 的影响@@
BMS 一般包括电池单元管理控制器@@ (CMC),主控中央单元或@@电池管理控制器@@ (BMC)。 CMC 采用多通道@@@@ IC (目前@@最多配备@@@@ 16 通道@@) 执行监控功能@@,BMC 负责控制每个@@ CMC。这类系统测量的主要参数包括温度@@@@、阻抗@@、电压和电流@@。
在考虑温度@@测量的情况下@@,负温度@@系数@@ (NTC) 热敏电阻@@是最常用的@@188足彩外围@@app
解决方案@@。通常@@,NTC 热敏电阻@@紧贴电池或@@模块壁@@,或@@电气接点连接以确定@@“热点@@”温度@@。随着热敏电阻@@温度@@上升@@,具有高灵敏度的@@ NTC 的阻值会下降@@,因为@@ NTC 电阻具备@@较大的负温度@@系数@@@@。温度@@的测量是通过采集普通电阻@@+热敏电阻@@的电阻网@@络上的电压@@,并将该模拟电压信号输送到集成在@@ IC 里面的@@ ADC 转换器进行后续处理完成的@@。精确的温度@@采集对@@电池的正常运行和整个@@ BMS 系统的安全来说必不可少@@。为了能精准地测量到温度@@@@,NTC 和测量电路又显得尤为重要@@。
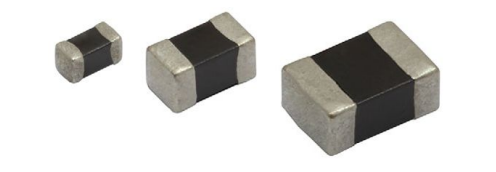
高压电池系统可以包括二十个或@@更多表面贴装@@ NTC 热敏电阻@@,这些@@热敏电阻@@位于包裹在组装的电池结构的柔性电路上@@。如果安装基板是@@ FR4 PCB,这些@@188足彩外围@@app
可以进行回流焊或@@波峰焊@@。

然而@@,一些柔性电路不能使用这些@@焊接技术@@@@,而是依靠局部加热的激光焊接@@,以避免损坏其他敏感部件@@。如果不能严格控制这种激光焊接工艺@@,就会导致陶瓷@@188足彩外围@@app 受到过量的热应力而开裂@@@@。
同样@@,整个电池系统在组装和工作中也会受到很大的机械应力@@。而且柔性电路板上的组件也会受到通过器件端子传导的扭力的影响@@@@,有些情况下甚至@@器件本身会直接承受压力@@,这些@@情况都会导致器件结构开裂@@@@。

这种故障@@取决于多种因素@@,使其难以检测@@,并且不太可能提前预测故障@@的出现@@。此外@@,多层陶瓷电容已经充分证明@@,实际@@188足彩外围@@app 故障@@ (188足彩外围@@app 开裂@@) 可能在系统完成安装部署之后的很长一段时@@间才出现@@。这种故障@@也可能是灾难性的@@,使得更换@@/维修的代价非常高@@。
NTCS 系列解决方案@@@@
为降低温度@@变化或@@使用柔性@@ PCB 可能产生的机械应力导致@@188足彩外围@@app
开裂@@的风险@@,Vishay NTCS 系列热敏电阻@@采用块状金属氧化物材料@@,配有固化环氧树脂封装的镍@@-锡镀层聚合物端子@@,而不是采用烧结的厚膜材料@@。这种解决方案@@提供柔性端子结构@@,其应力测试期间的表现显著优于其他端子材料@@,同时@@也显著优于来自于其它制造商的多层陶瓷结构器件的柔性端子方案@@。
由于使用柔性@@ PCB 电路板的电池管理系统的各个组件承受的应力不尽相同@@,因此@@采用能够吸收扭力和热应力的柔性端子解决方案@@可以显著减少潜在的现场实地故障@@@@,从而提高@@可靠性和使用寿命@@。
文章来源@@:Vishay威世科技@@